Tube Cleaning Solutions for “Shell & Tubes / Plates Heat Exchangers
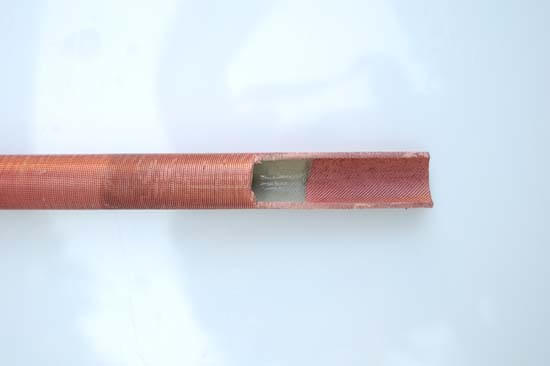
Tube Cleaning Solutions for Heat Exchangers
Whether dealing with water condensers in power plants or heating, ventilation, and air-conditioning systems in residential complexes, proper maintenance of equipment is essential for operational and economic efficiency.
The Ins and Outs of Tubes
A buildup of scale or harsh sedimentary substances in tubes can be lethal to the entire system. In the HVAC industry, this accumulation of contaminants is known as “fouling.” It’s the result of a gradual process that inevitably takes root during the equipment’s routine operations. Over the passage of time, total system replacement might be needed if fouling remains unchecked or tubes are insufficiently cleaned.
Reasons to Clean
- Biological debris, including mold and algae, constitute undesirable elements that can severely diminish an exchanger’s capacity. Bacterial development also adversely affects closed water systems; particularly those designed for hot water. Once the microorganisms have settled in, their acidic excrement corrodes the system’s metallic body.
- Corrosive gases can cause metal loss that can lead to leaks and system failure. The corrosion may be due to dissolved oxygen’s reaction with the system’s metal, low pH or any other pertinent factors. Regardless, metal oxides and sludge are the undesirable results
- Scale is essentially deposits of mineral particles formed in metals or other materials containing water engaged in temperature exchange. Generally, these particles are calcium carbonate or magnesium carbonate.
Solutions
The primary methods of tube cleaning are mechanical and chemical, often used jointly. Mechanical technology involves pump system launcher guns that propel cleaning material projectiles — foam pellets, coil brushes and plastic or metal scrapers — into the tubes. Water jetting is a high-pressure water system with the nozzle mounted on a lance or gun. It’s heavily favored in power plants for boiler cleaning. Chemical plants employ it for tube cleaning.
Acid scale inhibitors combat scaling effectively. Tube cleaning chemicals commonly used are sulfamic and citric acids. They dissolve the scale deposits, rendering them to a flushable state.
Upsides and Downsides
Which tube cleaning method is superior remains debatable. Pros and cons exist for both types. One mechanical advantage is the equipment’s flexible shaft which facilitates bends and curves. Another plus is that more operator attention may be given to individual tubes. Also on the mechanical advantages side is the fact that minimal operator training is needed.
Specific disadvantages of mechanical cleaning warrant real consideration. The weightiest is cost. First, service and equipment are expensive. Secondly, the entire exchanger system must be dismantled for cleaning, extending downtime. Finally, the method is ineffective on heavy fouling.
Chemical cleaning is more effective for scale dissolution; its primary advantage. It also allows more thorough accessibility to the tubes. Disadvantageously, the chemical method poses potential health and safety hazards. Also, it is highly corrosive to metal and like materials, necessitating a higher degree of training for its handlers to ensure proper use.